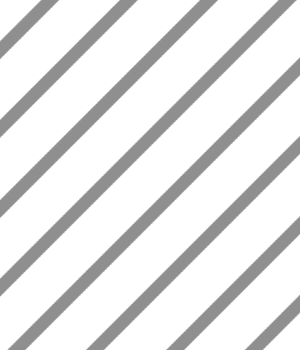
The manufacturing process: ROTOMOULING
Rotational moulding is a technique for manufacturing hollow plastic bodies. The rotational moulding process consists of four phases.
Loading the plastic material (in micronised form) into the mould:
Powder of a thermoplastic polymer is loaded into a mould. Before each cycle, the amount of powder is calculated according to the desired thickness. Rotational moulds are made in two or more removable parts. Rotational moulds are hollow, thin-walled and have good thermal and mechanical properties to withstand production cycles. Aluminium is often the preferred material for rotational moulding.
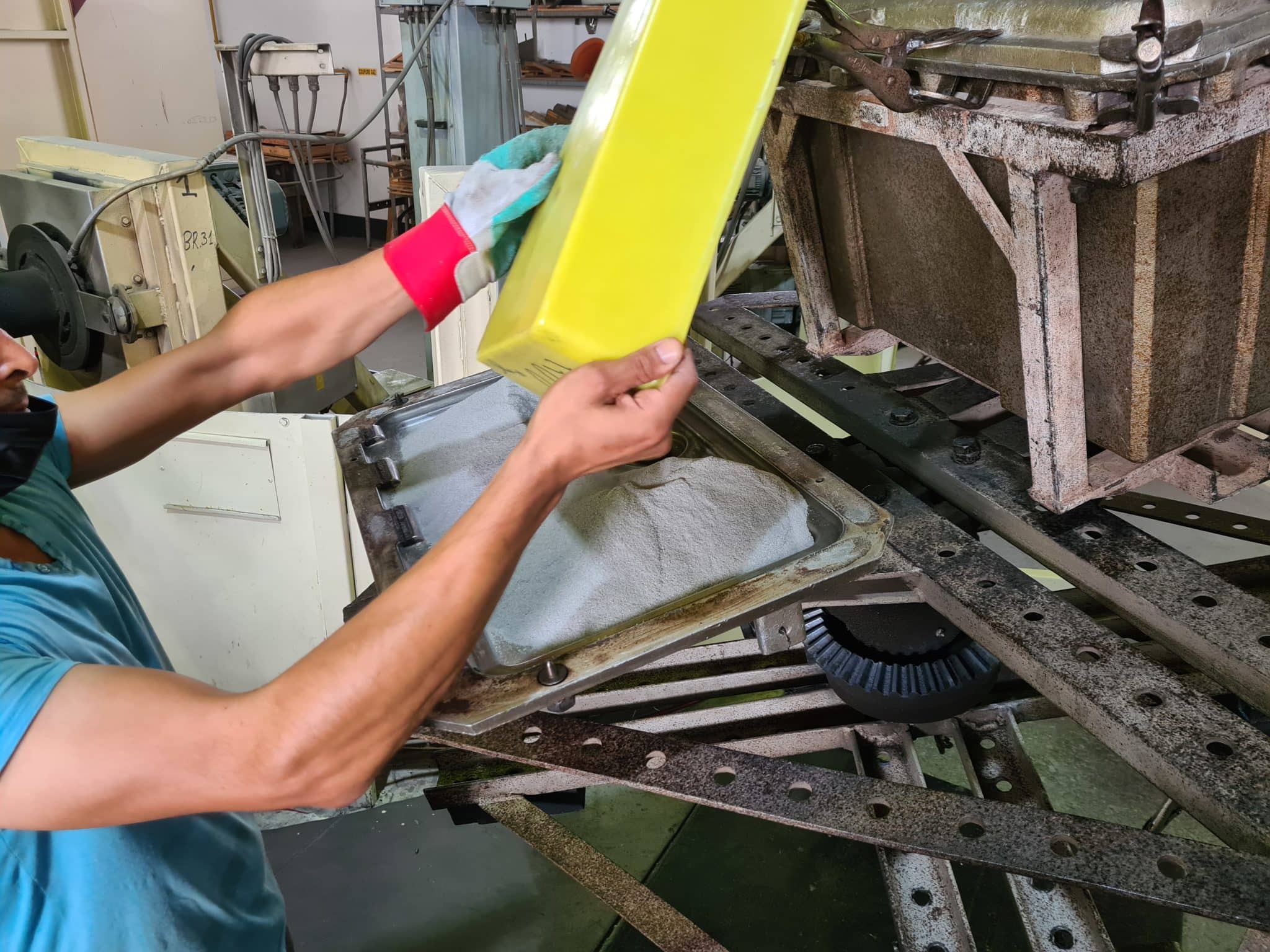
Heating
Once loaded and closed, the mould rotates along two perpendicular axes during a heating phase. Heat is supplied by gas burners with air circulation.
Cooling
In this stage, the mould, still rotating, is taken out of the oven to be cooled. Water, cold air or a combination of both ("misting") is used to cool the mould and thus the melted material.
Removal from the mould
The part is finally demoulded when the internal air temperature is sufficiently low. The connections between the upper and lower part of the mould are then opened and the part is extracted, reproducing exactly the internal architecture of the mould.
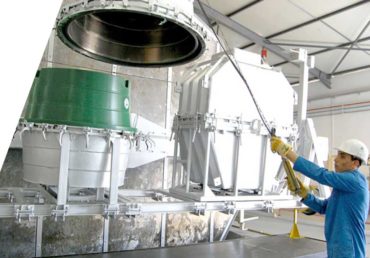